Work Order Management
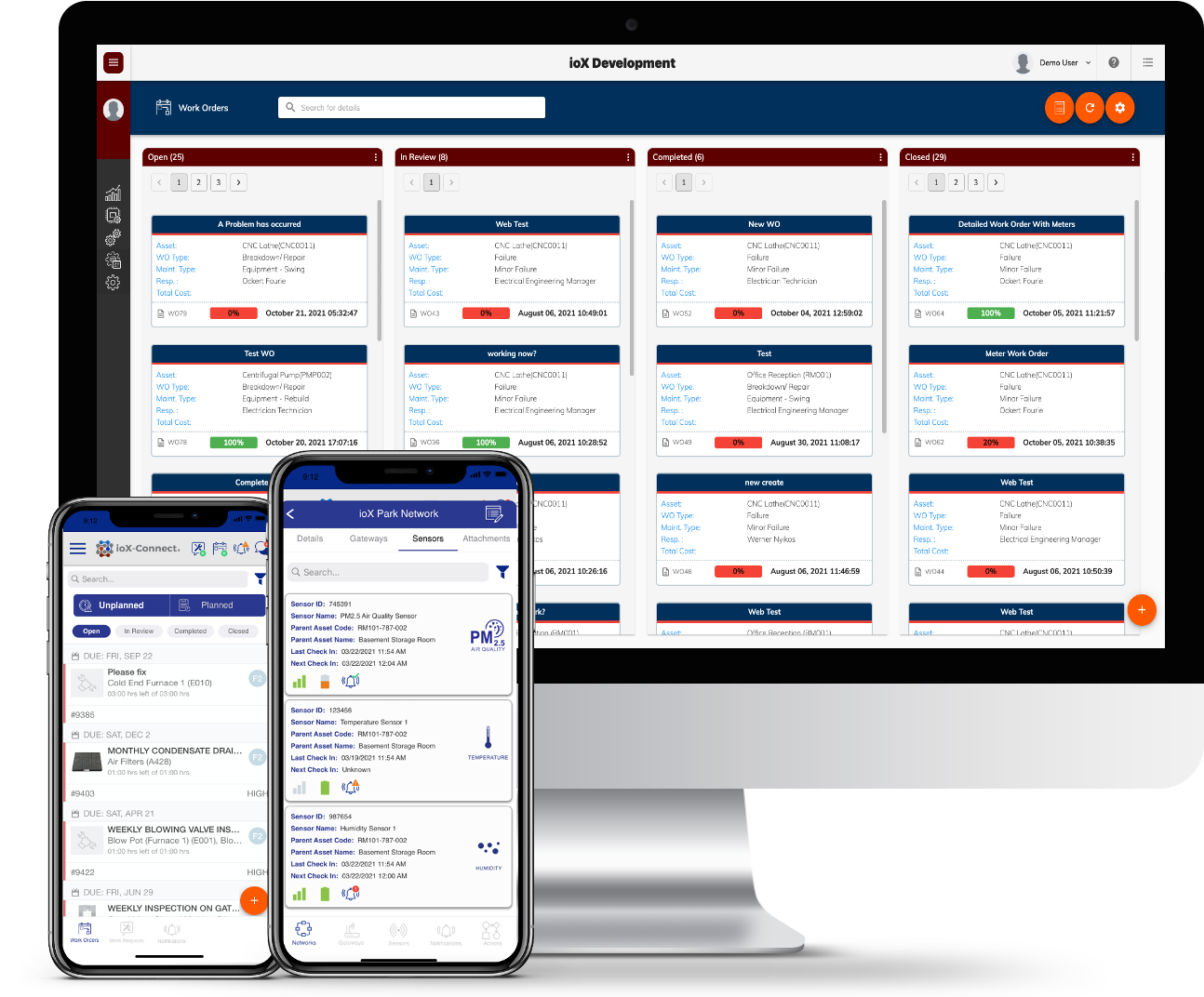
Optimize Your Maintenance Workflow with ioX-CMMS Work Order Management
Simplify your maintenance processes with ioX-CMMS’s powerful Work Order Management module. Designed to handle everything from creation to completion, our system ensures your team stays organized, accountable, and efficient. Whether you’re managing routine maintenance or urgent repairs, ioX-CMMS helps you track tasks, manage resources, and reduce downtime.
Cloud-Based & Hassle-Free Work Order Management
Streamline maintenance with ioX-CMMS’s Work Order Management, keeping your team organized and efficient while managing tasks and reducing downtime.
- Work Orders
- Multi-Tasking
- Pass/Fail and Flag Checklists
- Track Parts and Labor
- Failure Code Management
- Printable Work Orders
Easy Work Order Creation
Effortlessly create comprehensive work orders to ensure tasks are documented and assigned promptly. Our intuitive interface allows for quick data entry, ensuring that no detail is missed.
- Quickly generate detailed work orders with minimal effort. Add essential information such as equipment details, priority levels, and due dates.
- Create work orders on the go with mobile accessibility, ensuring no task is overlooked.
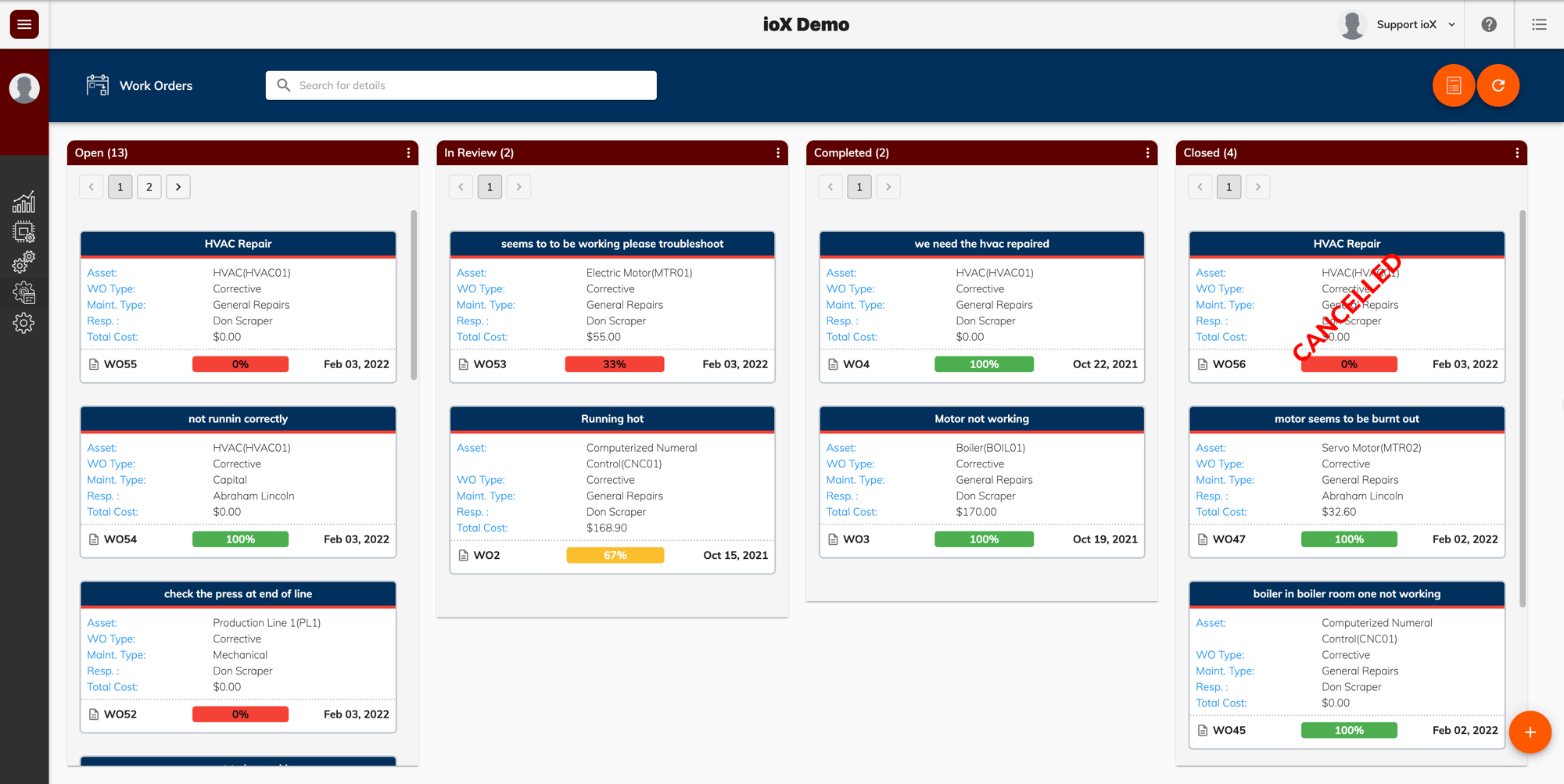
Multi-Tasking Capabilities
Streamline complex maintenance tasks by consolidating multiple activities within a single work order. Assign tasks individually to optimize efficiency and accountability.
- Enhance productivity by adding multiple tasks to a single work order.
- Assign each task to different team members, ensuring the right people handle the right tasks.
- Add specific checklists, labor requirements, and parts needed for each individual task.
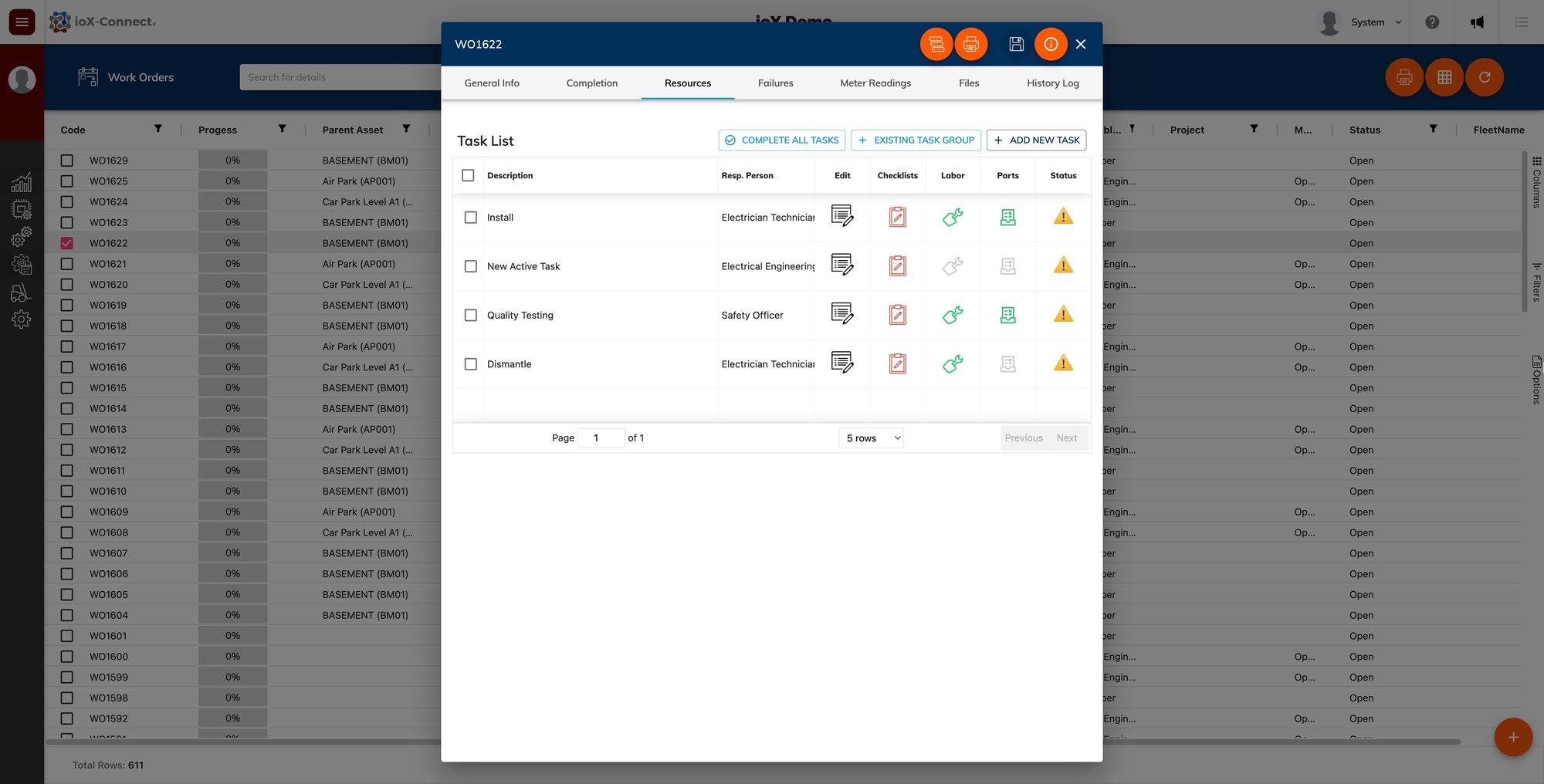
Pass/Fail and Flag Checklists
Ensure quality and compliance with customizable checklist options. Pass/Fail and Flag capabilities make inspections thorough and actionable.
- Incorporate Pass/Fail and Flag checklist items to simplify quality control and ensure thorough inspections.
- Easily identify and flag issues that need follow-up or corrective action.
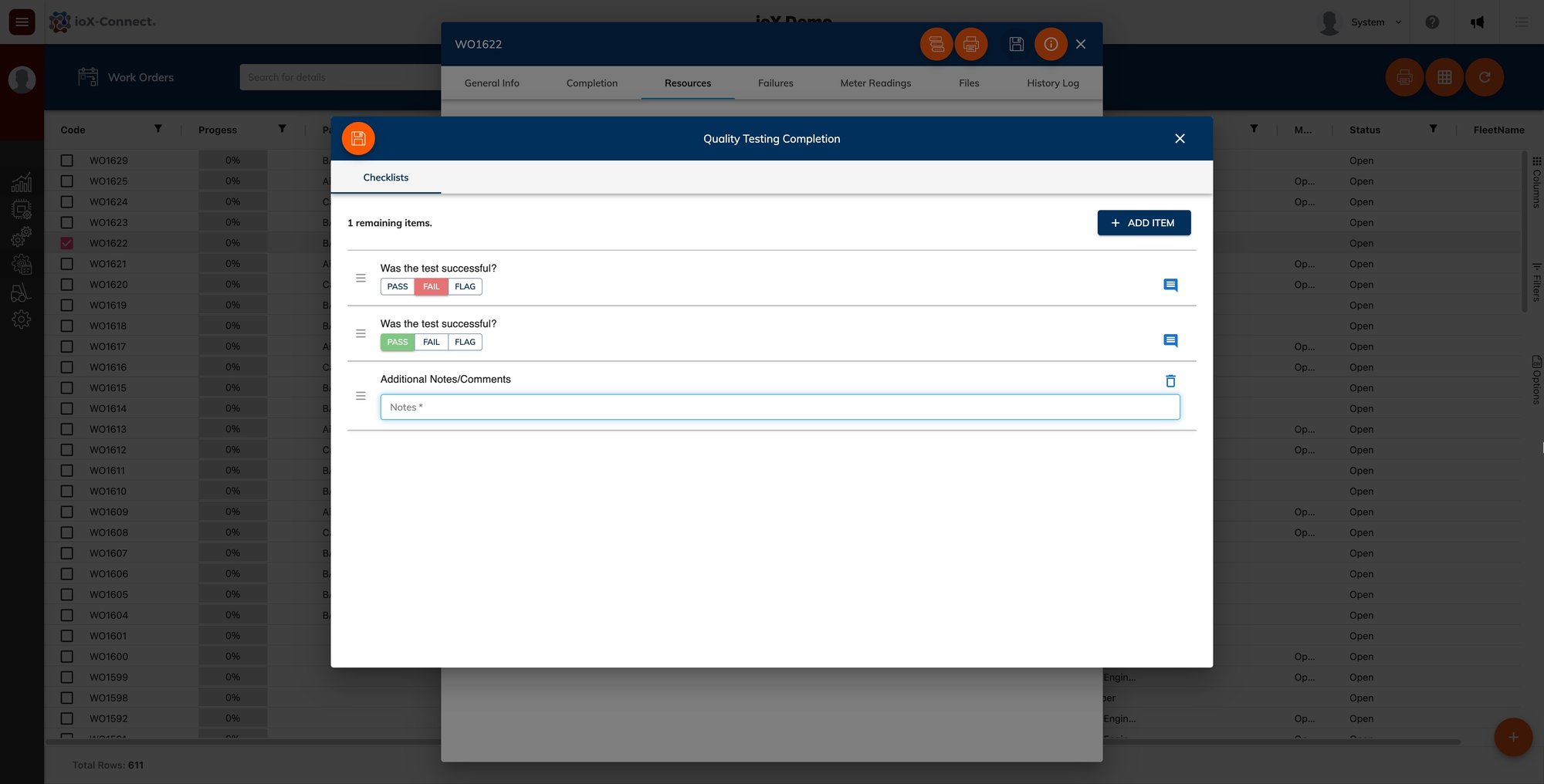
Track Parts and Labor
Gain visibility into maintenance costs by tracking parts and labor directly within each work order. Improve budgeting and resource allocation with precise data.
- Capture detailed information about parts and labor used for each work order.
- Track maintenance spend to gain insights into operational costs and improve budgeting.
- Capture different labor rates such as Normal Time, Overtime, and Double Time for accurate cost tracking.
- Ensure accurate record-keeping for audits and cost analysis.
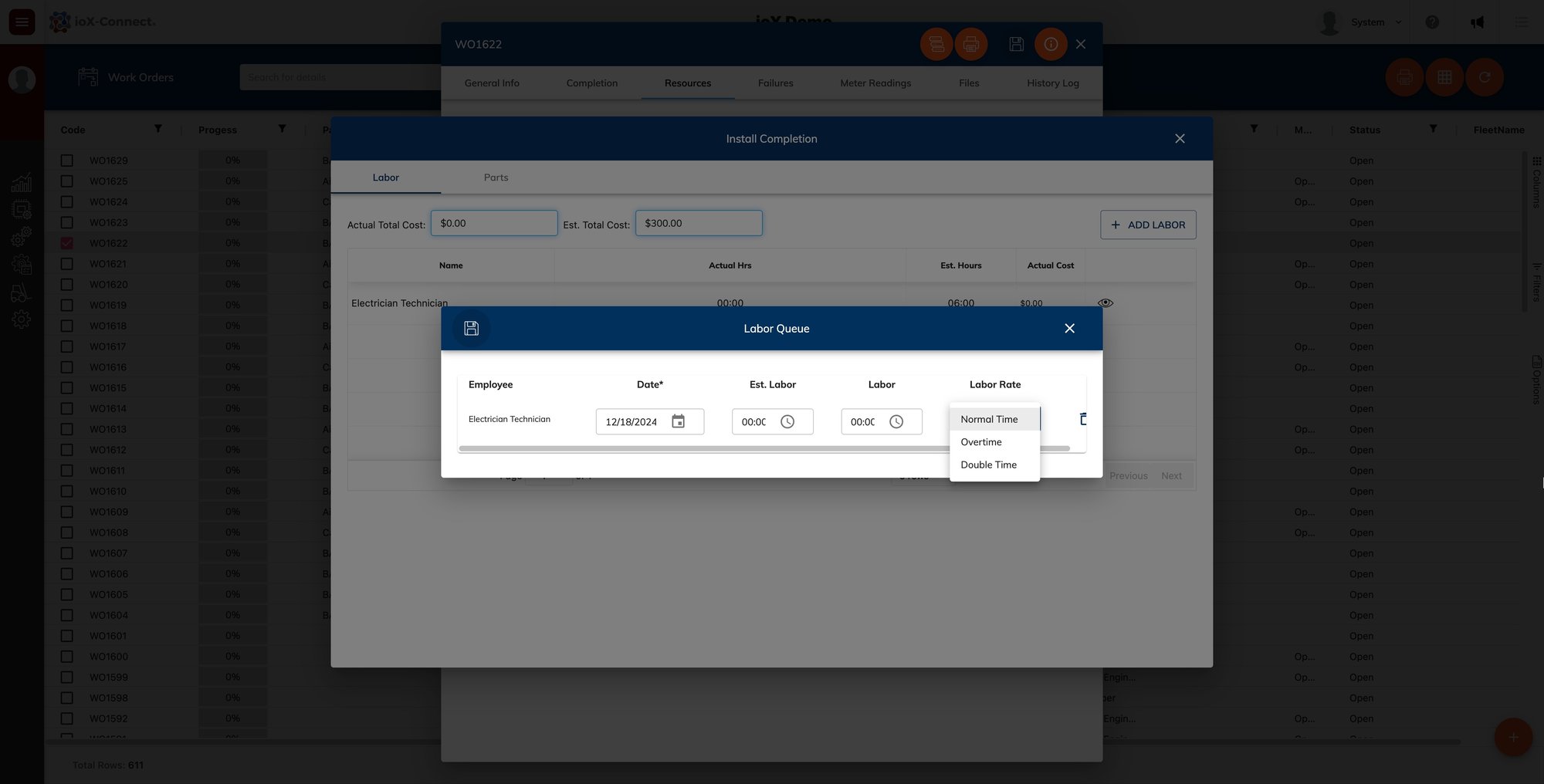
Failure Code Management
Diagnose recurring issues efficiently by capturing failure codes. Analyze trends to enhance equipment reliability and reduce downtime.
- Capture and document equipment failures using failure codes.
- Easily categorize and analyze failure patterns to improve asset reliability.
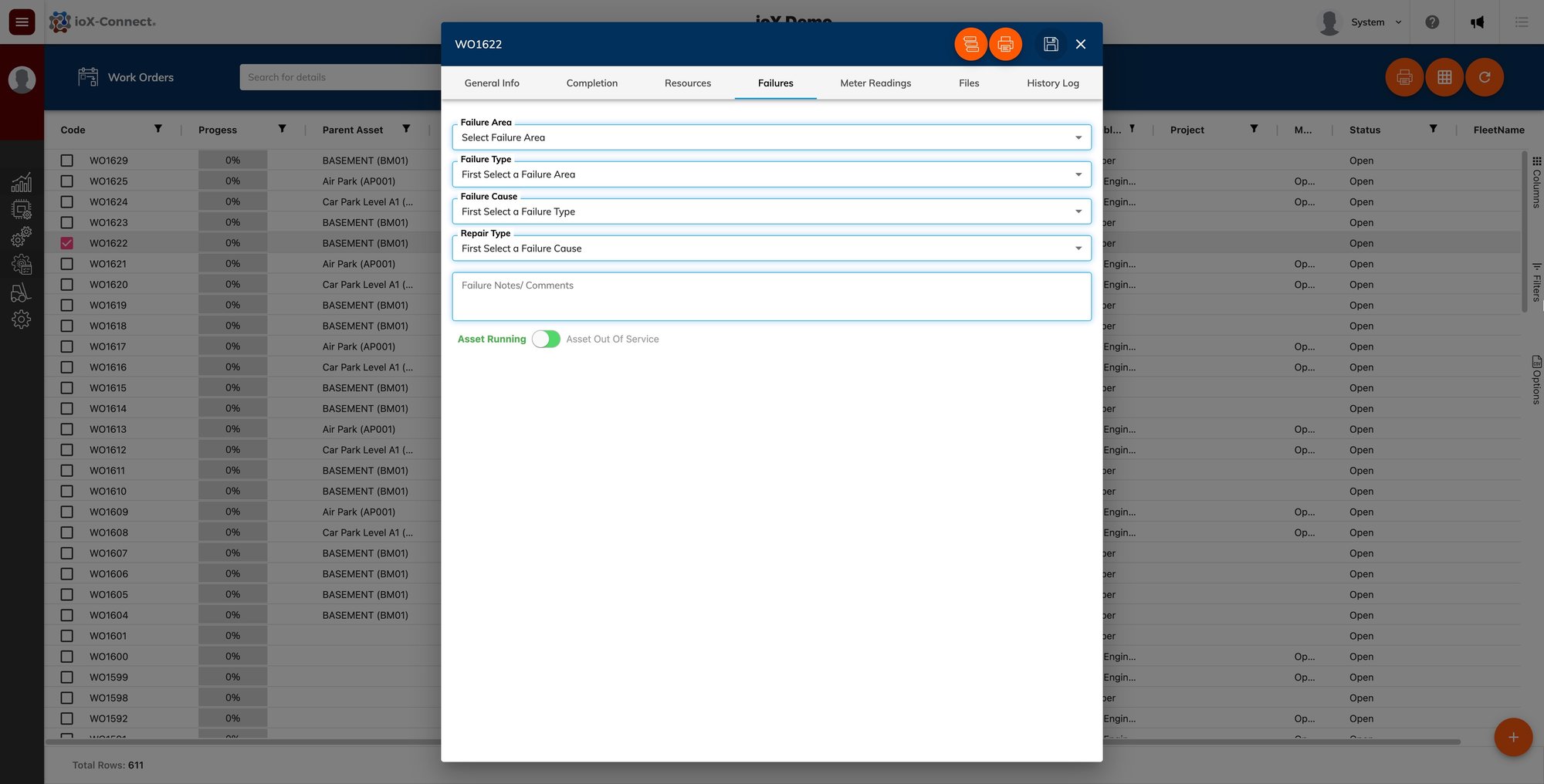
Printable Work Orders
Maintain operational flexibility with the ability to generate hard copies. Printed work orders ensure teams in the field can work seamlessly, even without digital access.
- For teams that require hard copies, ioX-CMMS offers the option to print work orders.
- Maintain flexibility with digital and physical documentation to suit your team’s needs.
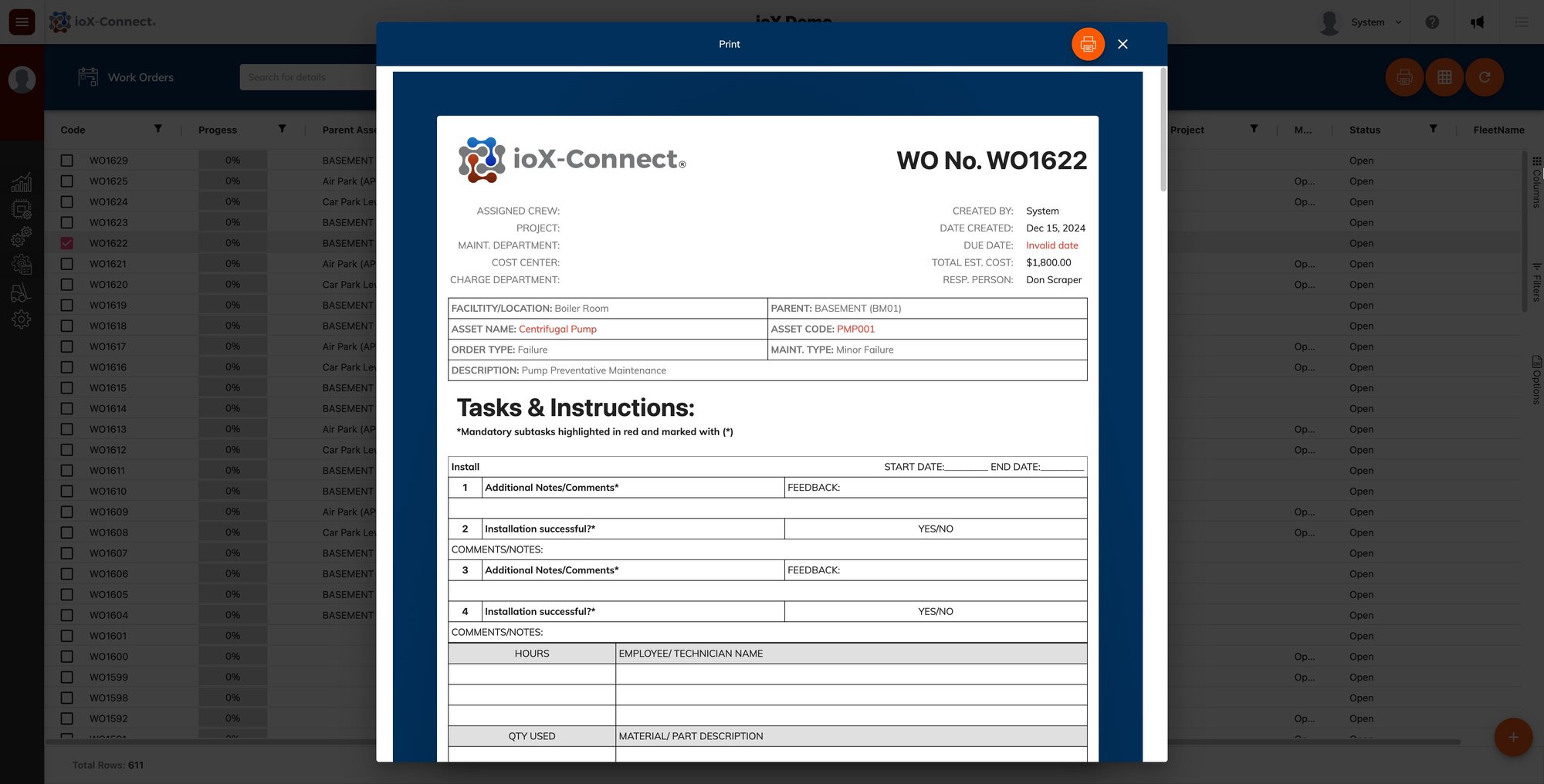
Why is Work Order Management Essential?
In today's fast-paced world, efficient work order management is more critical than ever. As the complexity of field service cases grows, maintaining organized workflows becomes a vital priority.
- Boost Productivity: Proper management reduces response times, ensuring tasks are completed accurately and on time, which significantly boosts productivity.
- Enhance Customer Satisfaction: Timely service enhances customer trust and loyalty. Research shows that 88% of customers are more likely to repurchase from companies providing excellent service.
- Optimize Resources: By efficiently allocating tasks, your team and assets can operate at peak performance, minimizing downtime and cutting operational costs.
- Ensure Compliance: Detailed record-keeping of service activities ensures adherence to industry standards, safeguarding against legal issues and potential fines.
With ioX-CMMS’s Work Order Management, you not only keep your team organized but also ensure compliance and customer satisfaction, paving the way for sustainable success.
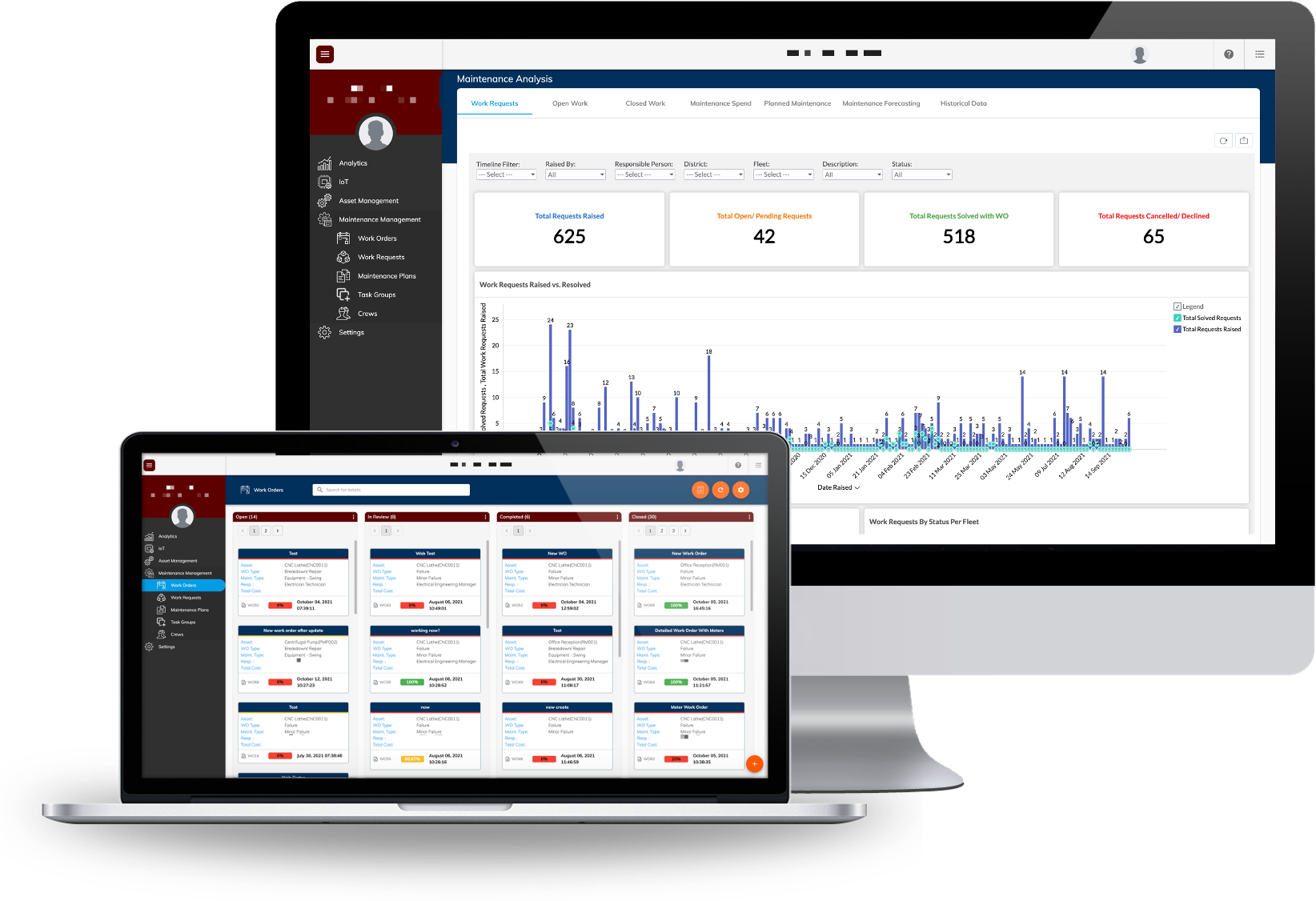
Major Fracking Company
VP Maintenance Management
"ioX-CMMS is a game-changer in the maintenance management industry. It has helped us reduce equipment downtime and optimize our manpower. Highly recommended!"
Pharmaceutical Manufacturer
Engineering Manager
"ioX-CMMS is a top-performing maintenance management solution in the market. Its innovative tools and exceptional service make it a must-have for any business."
Connected
Designed specifically for IoT and mobile applications. Integrates with sensors, meters, PLCs, SCADA, ERP, MES, and nearly all corporate systems and solutions.
Fast
ioX-CMMS is quick to implement and use, with tools enabling setup in days and work orders in hours or seconds.
Smart
Our Dashboards and Analytics excel, offering standard options for basic needs and Custom Analytics for complex requirements.
Mobile
Our iOS app enables field technicians to manage work tasks and record job details effortlessly, designed for ease of use even for beginners.
Trusted by customers across multiple industries
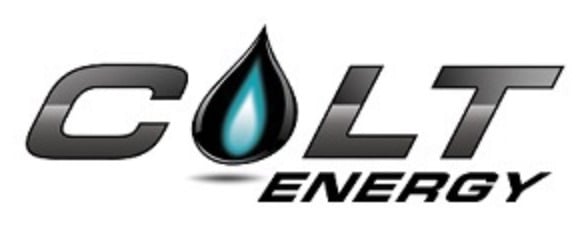
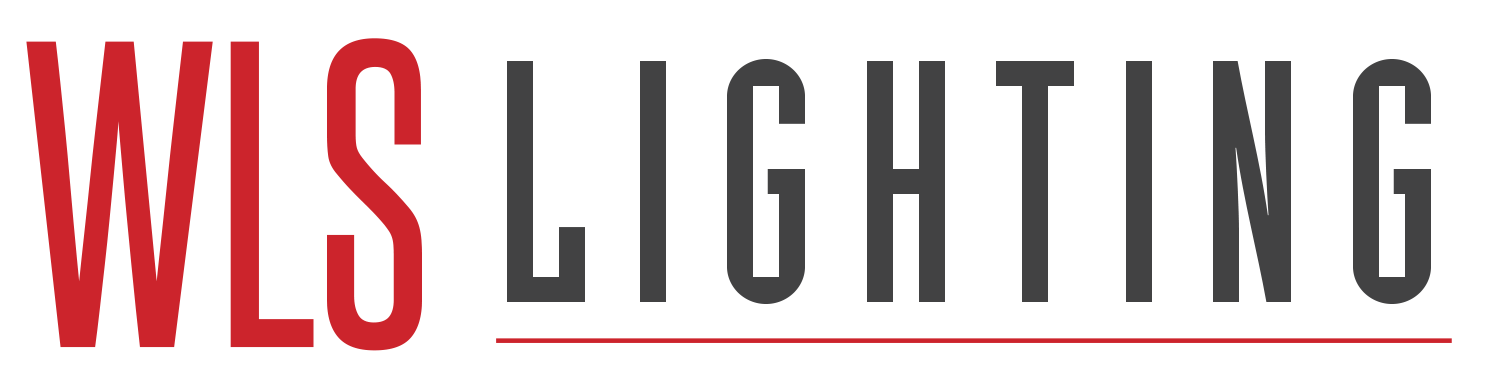
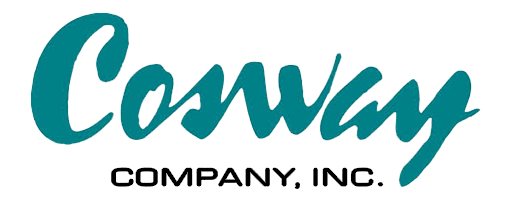
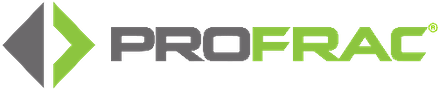
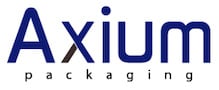
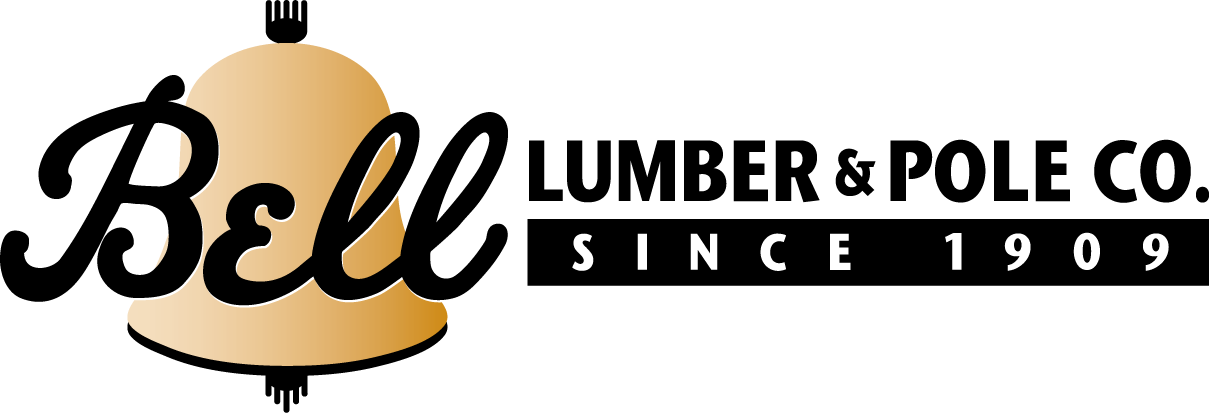
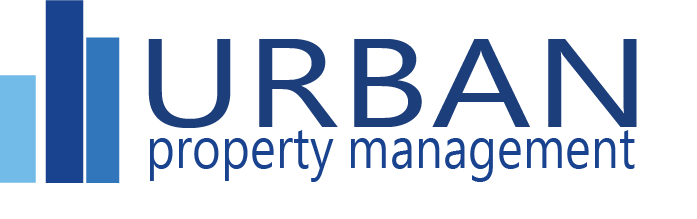
Frequently Asked Questions About CMMS
Have more questions about how a CMMS can transform your maintenance operations? We’re here to help! Explore our FAQs for quick answers to common questions, or feel free to reach out to our team for personalized assistance. Let us guide you toward the right solution for your business needs.
A Computerized Maintenance Management System (CMMS) is software that helps organizations manage and streamline maintenance operations. It tracks work orders, schedules preventive maintenance, monitors assets, and provides analytics to improve efficiency and reduce downtime. For a more in depth look at what is a CMMS, check out our What is a CMMS Informational Page
A CMMS centralizes maintenance data, allowing users to create work orders, schedule tasks, track asset performance, and access real-time insights. Technicians can update task statuses, log maintenance activities, and access manuals or checklists, ensuring smooth operations.
Effective work order management is essential for efficient field service operations. Here are some practices to adopt for success:
-
Consistency through Standardization:
- Implement uniform processes and protocols to maintain consistency and reliability.
- Establishing these standards minimizes errors and boosts operational efficiency.
-
Clear Communication Channels:
- Foster open and timely communication among teams and with customers.
- Ensure everyone is informed about responsibilities, updates, and changes to work orders, aligning expectations and accountability.
-
Continuous Training and Development:
- Invest in regular training sessions to equip your field teams with up-to-date skills and knowledge.
- Utilize third-party learning platforms to ensure teams can swiftly and effectively manage work orders.
-
Embrace Continuous Improvement:
- Monitor and refine workflows regularly to pinpoint improvement areas.
- Implement changes that align with evolving organizational goals and enhance service delivery.
-
Leverage Advanced Technologies:
- Integrate AI and machine learning to access real-time data, predictive insights, and automation.
- These technologies streamline decision-making and enhance operational efficiency.
-
Utilize Customer Feedback:
- Gather and integrate customer feedback into the management process.
- Tailoring services based on customer insights helps to fulfill their expectations and elevate satisfaction.
Incorporating these strategies ensures a robust framework for managing work orders, propelling your field service operations toward sustained success.
Work order management, while offering various benefits, often presents multiple hurdles. To master these challenges, strategic planning is essential. Let's explore some of the most common obstacles:
-
Diverse Service Requests: Service requests can differ significantly in terms of complexity and urgency. Handling such diversity effectively requires a robust and adaptable management system that can cater to a range of needs without compromising efficiency.
-
Efficient Scheduling: Effective scheduling is integral for optimizing resources and minimizing downtime. Finding the right balance between the availability of personnel and equipment, along with the fluctuating demands of service requests, is a complex yet crucial task.
-
Unexpected Disruptions: Plans often go awry due to unforeseen events. Successful work order management hinges on the ability to swiftly adapt to such changes, ensuring service delivery remains consistent and uninterrupted.
-
System Integration: Organizations typically rely on multiple systems for various operations. Seamlessly integrating work order management with these systems is essential. Without proper integration, crucial data may become siloed, limiting access and affecting productivity, especially for mobile workers.
-
Keeping Pace with Technological Advancements: The rapid evolution of technology means constant updates are necessary to maintain a competitive edge. This ongoing process requires investment in both training and technology, entailing additional time and financial resources.
Addressing these challenges with a strategic approach can significantly enhance the efficiency and effectiveness of work order management processes. Each obstacle demands a tailored solution, but overcoming them will lead to superior operational performance.
Work order management is a systematic approach to handling service requests and can be divided into several key types. Each type addresses various needs and situations, providing solutions tailored to specific maintenance challenges.
1. Preventative Maintenance
Preventative maintenance aims to avert potential issues by scheduling regular checks and upkeep. The goal is to minimize downtime and costs by identifying and fixing small problems before they escalate.
2. Proactive Maintenance
Proactive maintenance is focused on enhancing equipment reliability by delving into the root causes of failures. This approach not only prevents immediate issues but also improves long-term operational effectiveness.
3. Predictive Maintenance
Leveraging real-time data and advanced analytics, predictive maintenance forecasts potential equipment failures. By anticipating problems, businesses can prevent them from occurring, thus saving on repair costs and avoiding disruptions.
4. Reactive Maintenance
Reactive maintenance addresses unexpected equipment malfunctions requiring immediate attention. By responding to these unscheduled needs promptly, essential systems are quickly restored to full functionality.
5. Emergency Response
In situations where safety or operations are critically impacted, emergency response work orders take precedence. These orders ensure that issues like floods or major malfunctions receive swift attention to mitigate risk and operational downtime.
6. Inspections and Audits
Regular inspections and audits are conducted to verify compliance with safety and operational standards. They help identify and mitigate potential risks, ensuring that all processes meet regulatory requirements and maintain high standards of safety and efficiency.
Each type of work order management serves an essential role in maintaining the overall health and longevity of equipment and systems, tailored to address various operational demands efficiently.
A CMMS improves maintenance efficiency, reduces unplanned downtime, extends asset lifecycles, and enhances compliance. It also provides data-driven insights for better decision-making and streamlines communication between teams.
Improved Efficiency: By centralizing processes and data, field service technicians can complete more tasks quickly and accurately. Automated workflows minimize administrative tasks and eliminate the need to search for customer or asset details, ensuring that operations run smoothly.
Enhanced Customer Satisfaction: Delivering timely and effective maintenance boosts customer happiness and loyalty, a direct result of efficient service management.
Optimal Resource Usage: Effective allocation and management of resources ensure maximum utilization of workforce and equipment. This not only reduces waste and emissions but also supports sustainability initiatives.
Accurate Reporting and Analytics: A CMMS provides robust data that can be analyzed to uncover trends and measure performance, empowering organizations to make informed decisions and continually improve strategic planning.
Reduced Downtime: By actively managing work orders, companies minimize equipment downtime, keeping critical systems operational and avoiding costly disruptions, especially in industries like utilities and manufacturing.
Improved Accountability and Transparency: Clear task assignments and responsibilities foster a culture of accountability. Managers gain visibility into ongoing and completed tasks, helping identify bottlenecks and allocate resources more effectively.
Incorporating these benefits, a CMMS not only enhances operational efficiency but also drives overall organizational success.
CMMS software is used by maintenance managers, technicians, and facility managers across industries such as manufacturing, healthcare, hospitality, utilities, and logistics to manage equipment and facilities effectively.
While both systems manage assets, a CMMS focuses on maintenance operations, such as work orders and preventive maintenance. Enterprise Asset Management (EAM) provides broader asset lifecycle management, including procurement, inventory, and financials.
Yes, a CMMS like ioX-CMMS supports multi-site management, allowing users to track assets, work orders, and maintenance schedules across multiple facilities from a single platform, ensuring data segregation and efficient management.
A CMMS automates preventive maintenance scheduling based on time, usage, or condition triggers. This ensures timely inspections and repairs, reducing breakdowns and extending equipment lifespans.
Modern CMMS platforms, like ioX-CMMS, are designed with an intuitive interface, making them easy to use for technicians and managers alike. Mobile accessibility further enhances usability, allowing updates from anywhere.
A CMMS provides detailed reports on work order history, asset performance, maintenance costs, technician productivity, and compliance metrics. These insights help optimize maintenance strategies and improve ROI.
To choose the best CMMS, consider your organization's size, industry, and specific needs. Look for features like work order management, preventive maintenance, multi-site support, mobile access, and robust reporting. A scalable and customizable solution like ioX-CMMS is ideal for businesses of all sizes.
When selecting work order management software, several key factors should guide your decision:
-
Scalability: Ensure the software can grow with your organization, accommodating increasing volumes of work orders. Scalability is crucial for maintaining effectiveness as your operational needs evolve.
-
Integration: Opt for software that integrates smoothly with existing systems such as ERP and CRM. Seamless integration is vital for creating a unified workflow and reducing administrative overhead.
-
User-friendliness: Intuitive and easy-to-use tools are essential to minimize the learning curve for your team. User-friendly software enhances adoption and reduces training time.
-
Mobile Access: This feature allows field technicians to receive and update work orders on the go, even in areas with limited connectivity. Mobile access enhances efficiency and flexibility for a mobile workforce.
-
Real-time Tracking: Gain visibility into work order status and enable proactive management with real-time tracking and updates. This helps promptly identify and address any issues.
-
Reporting and Analytics: Advanced analytics features help monitor performance, identify trends, and make data-driven decisions, optimizing work order management processes.
By focusing on these factors, you ensure that your chosen CMMS will not only meet current needs but also adapt to future challenges, supporting your organization's growth and efficiency.
Our Products and Services?
We're here to help, do not hesitate to reach out to us by scheduling a quick call with one of our representatives.
Contact Us
Our customer service team is ready to assist you in exploring our offerings tailored to your business objectives.